Process automation is a technology (or rather a set of technologies) used for automating business processes. Essentially, the goal of process automation is three-fold:
- Reduce the work required to achieve the goal
- Centralize information
- Automate processes
Process automation helps reduce bottlenecks, discover errors in the process, improve communication between departments, and, ultimately, achieve the goal faster.
This article will further discuss the main benefits of process automation and guide you through its history to show you how we got where we are today. But before that, let’s check out a quick example for process automation.
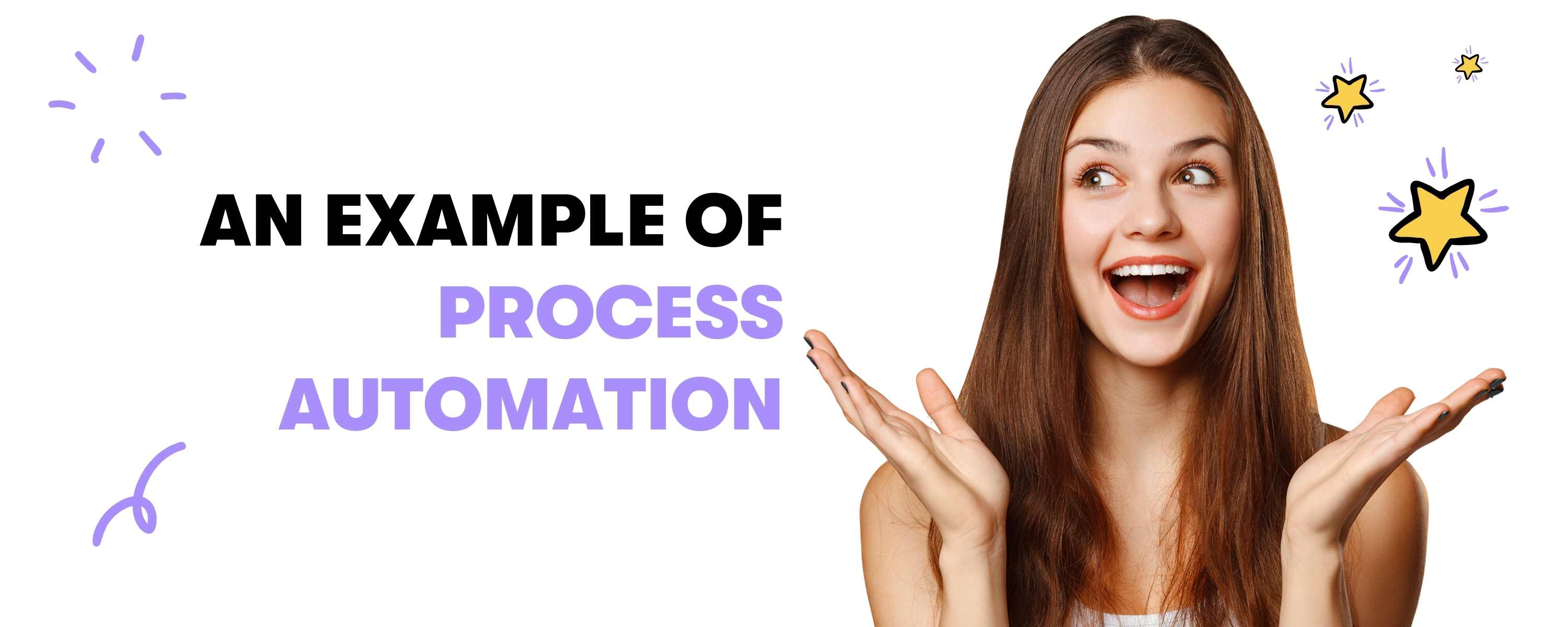
An Example of Process Automation
Nowadays, process automation can be applied to a wide variety of business processes. Still, we decided to give you an example of a simple process that every business has to deal with — invoice approval.
Invoice approval is the process of approving invoices before processing payments. It can sometimes have several steps, and here’s how they are automated.
- Receiving the invoice — The first step is simply getting an invoice from a vendor or supplier.
- Verifying the invoice — After you get the invoice, the dedicated staff member will have to check it and verify, usually by matching the invoice number with the purchase order. This is a step that can be completely automated.
- Addressing irregularities — If there’s something irregular with the invoice (such as missing information or price discrepancies, the invoice has to be sent to the relevant party that will address these irregularities. Process automation can help automate this step completely, check the entire invoice, and send it to whom it may concern.
- Approving the invoice — Once everything is sorted out, the invoice needs to be approved by the relevant personnel. Process automation can also jump in and automate sending the invoice for approval.
- Releasing the payment — The vendor is paid by the person in charge for the payments once the invoice is approved.
- Bookkeeping — There’s a permanent record added to your organization’s books once the payment is made.
Process automation can completely automatize the process, and involved parties only have to do the final step — approve the invoice (or address the irregularities, if there are any).
Invoice approval is one of the simpler processes, and there are several workers involved in a six-step procedure, meaning it can become quite tedious. Some processes are much more complex and include dozens of workers.
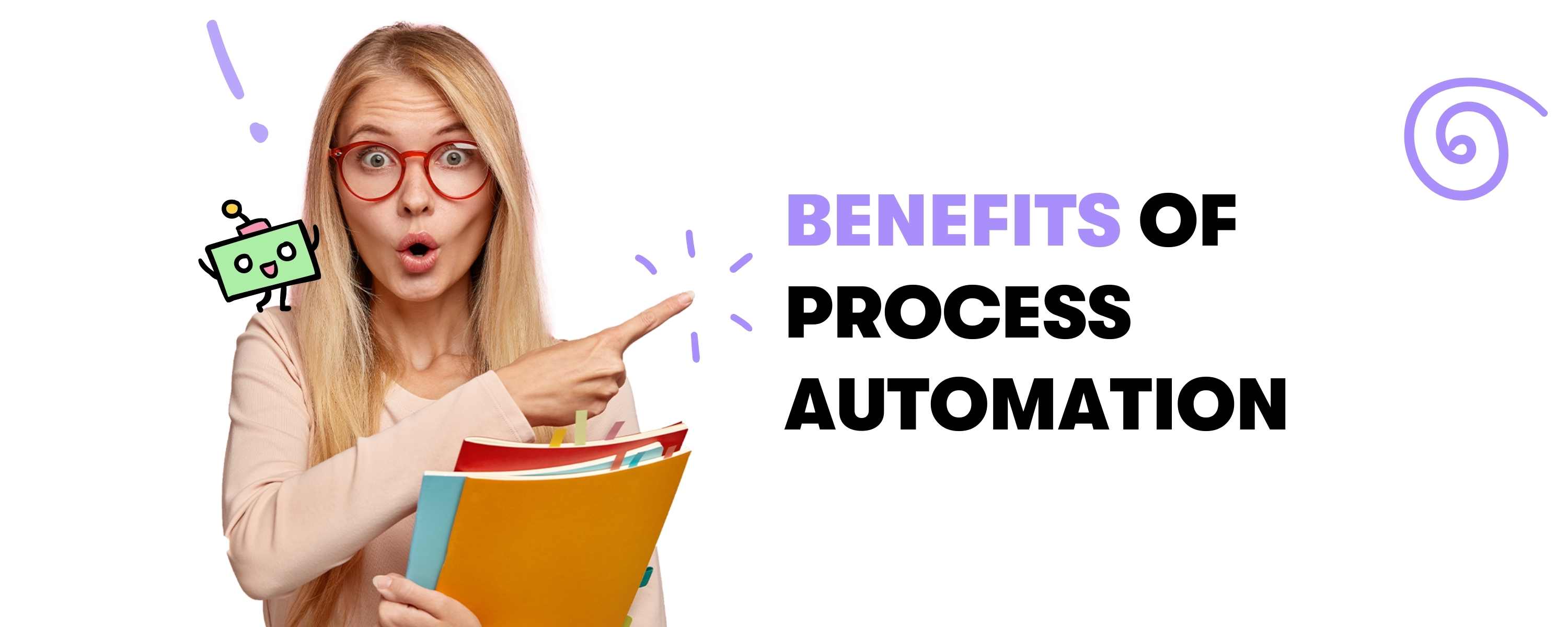
Benefits of Business Process Automation
Process automation comes with plenty of benefits. Here are the major ones:
- Reduced costs – Businesses can reduce up to 59% of costs by letting process automation do the heavy lifting.
- Improved productivity – You can reach your business goals faster and create better outcomes after automating processes that can be automated.
- Better staff utilization – Your staff can focus on more meaningful work instead of wasting hours — or even days — doing something that can be easily automated.
- Error reduction – To err is human, meaning we all make mistakes here and there, which can sometimes negatively affect your business. The good news is that this cannot happen once you automate the process and let computers do their job.
- Management transparency – Managers often get lost in everyday operations that they forget the big picture. Once all business processes are clearly defined and optimized, it becomes easier to understand the business and get ideas for further improvements.
- Reduced compliance concerns – Once you create an automated business process, you’ll cover all steps and ensure you’re meeting all internal and external standards.
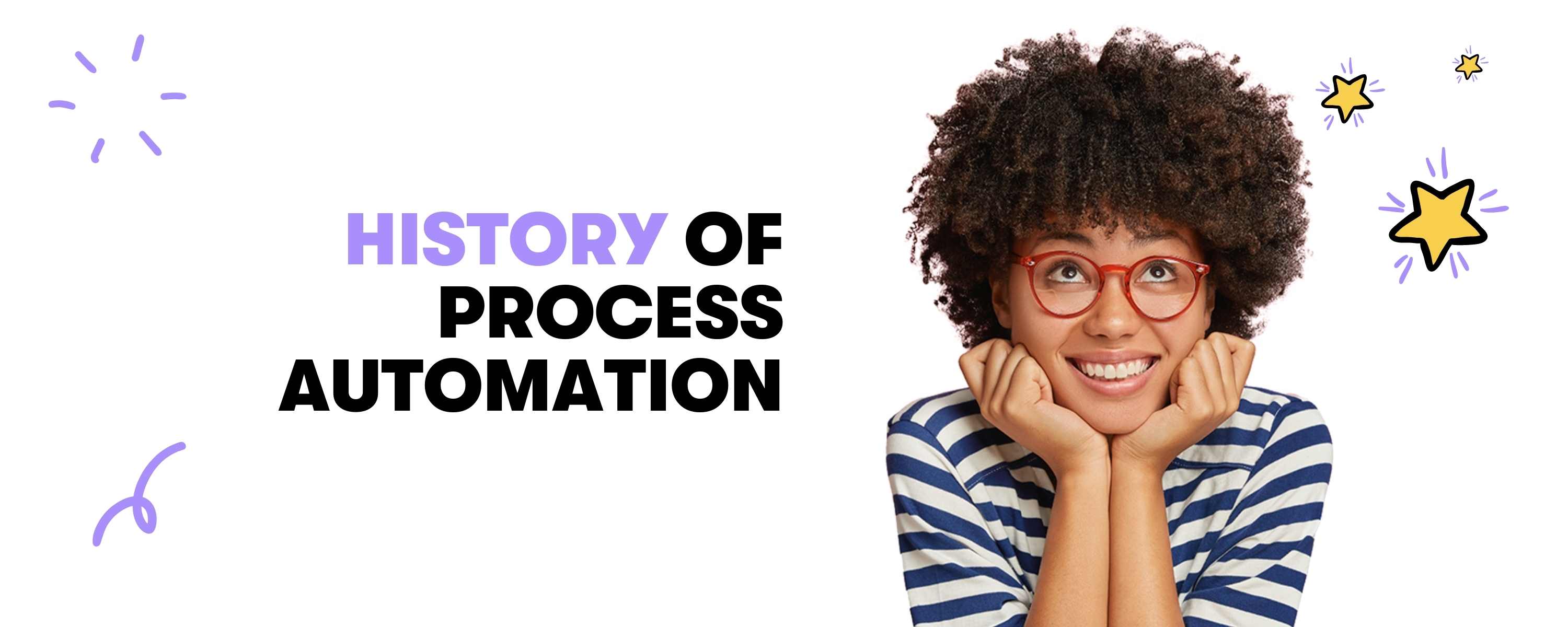
History of Process Automation
Automation may seem like a buzzword that has been used for a couple of years, but it’s actually much older than that. We have to look at the bigger picture and ask — when did automation really start?
Since the dawn of humankind, we have had this innate need to do things faster and with less effort. For thousands of years, we’ve been developing tools that made safer, more consistent, faster, and better. These tools have been further improved, remodeled, or entirely reimagined throughout history.
More than 2,000 years ago, the ancient Chinese made trip-hammers powered by waterwheels. Ancient Greeks also experimented with steam-powered motors. All in all, many ancient civilizations showed that the concept of automation has been evolving side-by-side with our society.
We made significant steps forward in the 19th century and the industrial age when inventors displayed various machines that automated business tasks. For instance, Joseph-Marie Jacquard, the French inventor, came up with the concept of the programmable machine. His legacy was continued and popularized by Alan Turing, the legendary British mathematician and computer scientist. Besides deciphering the German Enigma code to reveal Hitler’s plans, Turing also developed the first computer.
The Birth of Process Optimization and Management
Like many other technologies and techniques, process automation had predecessors — process optimization and management. They are still an integral part when automating processes, as automation wouldn’t be possible without them. In fact, to make a good automated process, it’s necessary to have a good process to start with. If automation is applied to a bad process, it’s just a bandage to cover the wounds short term. It’s not a cure.
The early application of process optimization and management was seen in card manufacturing in the first half of the 20th century. The first and perhaps most popular example is that of an assembly line in Ford factories that paved the way for mass production. This was also a sort of standardization that enabled scaling production. Toyota later upgraded this model, naming it the Toyota Production System, the predecessor to Lean and Six Sigma.
Nowadays, some of these production processes that started with Ford are pretty much standard. It’s difficult to imagine big stores sticking to one-off production. Imagine buying jeans only to wait for hours for the workers to take your measures, preferences, obtain the necessary cloth, and produce jeans tailored for you.
We can make a parallel between the production line and the customer journey. In digital marketing, online customers have a journey from learning about your brand for the first time to buying your product and service.
There are steps they usually need to take to become a buyer, known as a customer journey. Process automation made it possible to streamline the journey and make it easy and convenient for customers to learn more about your brand and eventually buy it.
In a way, process automation is one of the components of the industrialization period of IT.
The Early Days of Process Automation
Process automation as such started to take off in the 1990s when the first automation solutions were developed. The major impact of early 90s software was the replacement of paper-based processes with electronic ones. Making processes digital instead of physical allowed businesses to harness computers’ power and improve all their operations.
In the late 90s, additional progress was made when automation software was enriched with additional features, including modeling tools, business rules, and more. They made it possible to analyze, model, and describe business processes and were another significant step in the path of process automation development.
The Rise of Robotic Process Automation
Some of the first companies to start offering RPA were Blue Prism, Ui Path, and Automation Anywhere. Most of these companies marketed their services around 2003, meaning RPA has been around for almost two decades. The first use of RPA was reducing costs in Business Process Outsourcing but later moved to other areas, including IT Outsourcing, Shared Services, and other business spheres.
Process Mining
Introduced by Wil van der Aalst, who also gave it a name, process mining focuses on discovering, monitoring, and improving processes. Think of it as an X-ray for processes in an organization.
Even though it was created in the early 2000s, process mining was popularized by Celonis, a company established in 2011 by Alex Rinke, Martin Klenk, and Bastian Nominacher. They started working on it while at the Technical University of Munich.
After Celonis bought Integromat, the IpaaS champion, it started combining process mining with IPaaS to discover new possibilities.
Cloud and IPaaS
IPaaS was the next big thing in automation after process mining. It stands for Integration Platform as a Service. It has been around since 2011 and was a response to many companies adopting cloud infrastructure and applications.
Essentially, IPaaS is a set of cloud-based services that help businesses integrate applications easily into their infrastructure. This facilitates sharing data and process automation further.
Low Code and No Code
Low Code Development Platforms have been emerging since 2011, and the term “low code” boomed after the Forrester Group publication in 2016. Essentially, the amount of code necessary to create a business process and set it into motion has been reduced significantly. In other words, businesses nowadays don’t need tech geniuses to automate processes, as some of them can be created without writing a single line of code (no code).
Intelligent Process Automation
Joining process automation with artificial intelligence was inevitable for improving automation in general. Even though AI has been actively researched since 1956, starting with a college campus at Dartmouth College, it has been heavily used in the last couple of years.
The first instance of intelligent process automation appeared around 2015, with the introduction of Cognitive RPA, which improved optical character recognition (OCR), natural language processing (NLP), and machine learning. This meant we were able to have a better handle of semi-structured and unstructured data, increasing the overall scope of robotic process automation. In fact, the RPA we know today is closely tied to intelligent process automation.

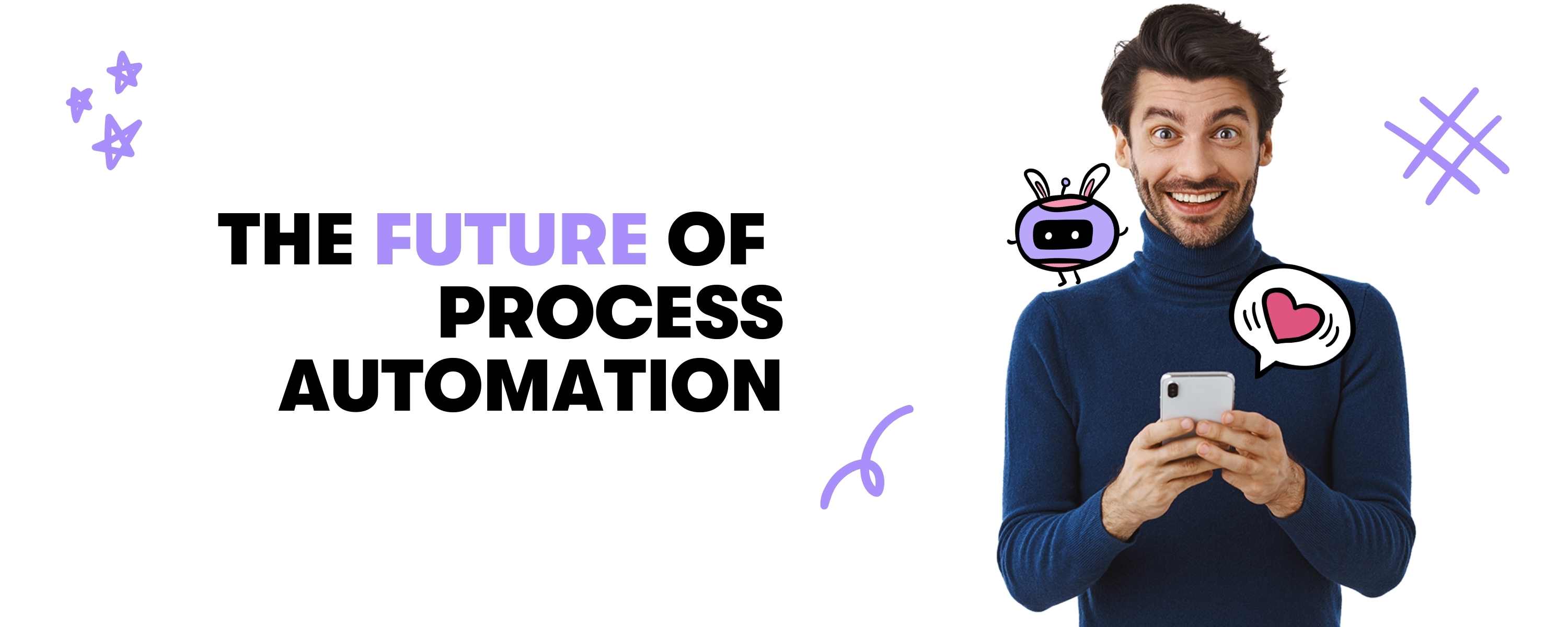
What Can We Expect from Process Automation in the Future?
New technologies and methods related to process automation keep appearing, and the two most important ones are Hyperautomation and Automation as a Service (AaaS).
The term Hyperautomation appeared first in 2019, and it was recognized as one of Gartner’s top 10 strategic technology trends in 2020. It denotes a set of technologies, including AI and ML that allow for optimizing business processes much better. In some cases, the term is used interchangeably with intelligent process automation.
According to Gartner, the global market for Hyperautomation-related tools and technologies will reach approximately $596.6 billion in 2022.
Automation as a Service is a type of Netflix-like approach to offering automation. For a monthly subscription, AaaS companies will set up the infrastructure for automation, analyze all your processes, and automate the ones that can be automated step-by-step. This is a perfect solution for both big businesses and companies on a budget that want to integrate process automation right away.

The Holy Trinity of Process Automation
A bad process will be a bad automated process. As already mentioned in the history part, automation is just a part of process management. To get the most from the automated process, you first need to make the process as optimized as possible.
People working on a process often cannot provide an answer to why they’re doing something the way they do. Even if they can, they are often surprised with the answer, learning that there might be room for further improvement. In other words, they start questioning whether there’s another way to approach the process to make it better.
Many process owners and other employees only start to question their process after opening up to the possibility of automating the process.
All in all, it’s necessary to get the most out of the process before automating it, and that’s why the holy trinity of process automation exists. It consists of the following three actions:
- Improve – The first step is to improve the process if there’s room for improvement. It includes educating your workers about business process management and regularly working on every step of the process to examine it and upgrade it if possible. It’s important to ask the following questions all the time: Why is something done the way it’s done? Can you improve it further?
- Eliminate – Processes evolve with technology, and some steps that made perfect steps a decade ago are nowadays obsolete and can be completely eliminated from the process. Alternatively, they can be moved to another place or incorporated in a way that makes more sense.
- Automate – The final step is to automate the process. Of course, modern automation tools allow us to automate only certain steps and have them cooperate with workers working on the process.
Conclusion: Should You Use Process Automation?
Most businesses nowadays either already use process automation or have an increasing need to do it. The main reason most companies choose to use it is the ongoing efficiency pressure, which basically revolves around cutting costs and generating higher net income. These are often considered the hard factors.
But whether a company should choose automation goes beyond that, as you have to take the soft factors into account as well. The first indicator you should consider is full-time equivalent (FTE). If it’s 0.3 FTE, meaning you can save approximately 12 hours of work per 40-hour workweek, then introducing process automation is definitely worth it. Of course, you need to take into account the costs and time required to automatize the process and decide if it’s more profitable than not using it at all.
You shouldn’t always base your decision on a single FTE measurement nor replace your workers with automation. Instead, the best long-term approach is to use process automation to help workers with repetitive and manual tasks to focus on more meaningful work. This could improve your overall employee satisfaction.
In addition to that, you can increase customer satisfaction, especially if they get your product or service much faster, thanks to automated processes.
Still not enough about process automation? Check out our free 200+ pages eBook full of concentrated knowledge about Process Automation!